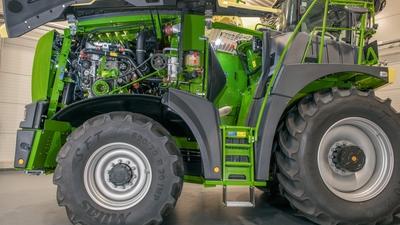
Adapter la puissance à l’organisation du chantier
Le premier paramètre à prendre en compte est la puissance moteur nécessaire. « L’offre en matière de puissance est vaste. Par exemple, chez Krone, nous commercialisons des machines de 490 à 1.156 ch », poursuit notre interlocuteur.
Le choix de la puissance moteur se définit en fonction de la surface de travail, du relief de la région ou encore de la structure du sol. L’organisation du chantier de récolte a aussi son importance, deux cas de figure pouvant se présenter : dans le premier cas, l’entrepreneur gère la totalité du chantier, avec son ensileuse, ses tracteurs et caisses d’ensilage, ainsi que son agrochargeuse pour tasser le silo. Dans le second cas, c’est l’agriculteur qui fournit des bennes et qui tasse lui-même le silo.
« Il est évident que cette organisation influe sur le débit de chantier, et donc sur les performances de l’ensileuse. Dans le premier cas évoqué, les capacités des différentes phases du chantier, qu’il s’agisse de l’ensilage, du transport ou de la prise en charge au niveau du silo, sont beaucoup plus importantes. Sans oublier que les différents chauffeurs, issus de l’entreprise agricole, ont l’habitude de rouler ensemble et disposent donc d’automatismes affûtés. Le choix d’une ensileuse puissante revêt alors un intérêt certain, contrairement à la deuxième situation qui verra le travail de l’ensileuse ralenti par de plus petits moyens de transport, des chauffeurs moins aguerris ou une limitation des capacités à l’entrée du silo. Tous ces critères déterminent en fin de compte la puissance du moteur mais aussi la largeur du bec, qui évolue en parallèle. »
L’achat d’une nouvelle ensileuse représente un investissement pour une durée moyenne de sept ans. Il est donc important d’estimer le potentiel de travail sur ces sept années. « Globalement, le profil-type des machines qui évoluent dans notre pays est le suivant : 35 % des machines vendues sont des engins d’environ
Choisir un bec conforme aux législations routières…
Puissance moteur et taille du bec sont donc étroitement corrélées mais il reste à déterminer le bon type de bec, comme le souligne Marc. « C’est en effet un point sensible. En Europe occidentale, cinq grands constructeurs d’ensileuses se partagent le marché, à savoir Krone, Claas, New Holland, John Deere et Fendt. Il faut par contre être conscient du fait qu’il n’existe que trois constructeurs de becs, non pas en Europe mais dans le monde entier, en l’occurrence Krone, Kemper et Claas. »
Pourquoi sont-ils si peu nombreux ? Tout simplement parce que l’élément le plus complexe à développer sur une telle machine est précisément le bec à maïs. « La raison en est que le maïs change toutes les années et en fonction des régions : il peut être grand, petit, versé, bien désherbé ou pas… Sans parler de spécificités variétales en tous genres qui peuvent compliquer la récolte. Il est donc très difficile voire quasiment impossible de développer un bec universel qui donnerait satisfaction à toute la clientèle mondiale ».
Le choix du bec doit aussi se faire en fonction du service fourni par son constructeur dans la région, les pannes et dommages pouvant en effet survenir sans prévenir. Notre interlocuteur souhaite par ailleurs attirer l’attention sur le respect des législations routières.
« Les critères d’homologation d’une ensileuse précisent que le poids total au sol est limité à 24 t, avec maximum 12,5 t sur un des deux essieux. Or, toutes les grosses ensileuses de 600 ch et plus, avec un bec de 10 rangs, dépassent ces seuils limites. C’est ce qui explique que tous les constructeurs ont conçu soit un système d’essieu, soit des roues de délestage sur leurs becs. »
« Chez Krone, nous avons mis au point une toute nouvelle génération de becs sur lesquels les roues de délestage restent sur le bec au travail. Sur les versions précédentes, il s’agissait d’un dispositif amovible qu’il fallait retirer dès l’arrivée au champ, avec comme inconvénients principaux des pertes de temps et souvent des difficultés à trouver un endroit où stationner le chariot… »
L’éclairage devant le bec est le second point important. Ce type d’éclairage est imposé par la réglementation pour circuler sur la voie publique. La plupart des constructeurs proposent soit des systèmes démontables, soit des systèmes d’éclairage et de protection à commande hydraulique ne devant pas être démontés au travail.
Les dispositifs amovibles peuvent paraître contraignants car il faut descendre de la cabine, retirer les broches, déposer le système dans le talus voisin… Quant aux systèmes hydrauliques, le principal défaut réside dans leur coût.
… et selon plusieurs critères financiers
Lorsque l’on s’intéresse au point de vue financier, le bec est un élément important dans le coût d’utilisation d’une ensileuse. Il faut donc s’y intéresser de près pour évaluer au mieux l’amortissement de la machine, en se référant notamment au coût moyen par hectare annoncé par le constructeur.
« C’est exact », renchérit Marc, « chaque bec a une construction qui lui est propre, avec des organes coupants, tels les couteaux et contre-couteaux, ou des organes d’entraînement différents des becs concurrents. Attention cependant, le coût par hectare transmis par le constructeur est une donnée moyenne. Il est impératif de le rapporter aussi aux spécificités régionales. Ainsi, si l’ensileuse est destinée à travailler sur des sols sableux, le coût d’utilisation augmentera sensiblement du fait que le sable usera plus rapidement les pièces qu’un sol argileux par exemple. »
Certains becs engendrent par ailleurs une consommation de carburant plus importante pour leur entraînement. « Le bec Krone est facile à entraîner, ce qui permet de l’arrêter et d’en inverser le sens de rotation à chaque bout de ligne afin d’éliminer l’accumulation éventuelle de feuilles et autres résidus. D’autres constructeurs en réduisent simplement la vitesse mais ne l’arrêtent pas, en raison d’une plus grande inertie ».
Préférer le rotor approprié à sa clientèle
Après le bec vient le choix du rotor dont le type et le nombre de couteaux conditionnent les performances de hachage. Il faut aussi être conscient que chaque rotor a une plage de travail idéale.
« Le nombre de couteaux détermine la longueur de coupe. Si je prends, pour exemple, le rotor Krone, avec 20 couteaux, la longueur de coupe idéale sera de 15 à 30 mm ; avec 28 couteaux, configuration la plus vendue en Belgique, la longueur de coupe idéale sera comprise entre 8 et 20 mm. Doté de 40 couteaux, il procure une longueur de coupe idéale de 4 à 10 mm, ce qui convient parfaitement à la biomasse, les stations de biométhanisation ayant un meilleur rendement quand la matière est coupée courte. »
Ceci pose d’ailleurs problème aux entrepreneurs qui ont deux types de clientèle aux exigences différentes : un éleveur qui veut une longueur de coupe de 12 à 15 mm et un biométhaniseur qui souhaite une coupe de 4 à 5 mm. Aucun rotor ne peut être performant à la fois à 20 mm et à 4 mm.
« Certains pensent pouvoir régler le problème en agissant sur le régime de rotation des rouleaux d’alimentation. S’il est vrai que l’on coupe plus long en faisant tourner les rouleaux d’alimentation plus vite et plus court en les ralentissant, d’autres inconvénients apparaissent rapidement : l’alimentation freine le flux de marchandise ou se fait par à-coups, le rotor est sous-alimenté ou sur-alimenté, ce qui rend la qualité du hachage plus aléatoire, et la consommation de carburant augmente. »
Il est donc très difficile d’avoir une machine performante à la fois pour l’alimentation animale et pour le biogaz. Il faut donc poser son choix en fonction de la demande majoritaire des clients.
Krone propose à la vente une solution originale permettant de couper à une longueur normale et à une longueur plus importante. Il s’agit de la boîte de vitesses Variloc sur le rotor : « Ce dernier tourne à 1.200 tr/min. Variloc permet d’abaisser ce régime à 800 tr/min en moins de trois minutes. Avec un rotor de 40 couteaux, on obtient une longueur de 4 à 5 mm à 1.200 tr/min et de 15 à 20 mm à 800 tr/min. Ceci peut constituer une solution, unique sur le marché, pour une clientèle mixte ».
Le nombre de couteaux en maïs va aussi déterminer la longueur de coupe en herbe puisqu’il est d’usage de retirer un couteau sur deux pour l’herbe : « Avec un rotor de 28 couteaux dont on a enlevé un couteau sur deux, on obtiendra une longueur en herbe de 40 mm, ce qui répond aux attentes des éleveurs au niveau de la structure. Par contre, avec un rotor de 40 couteaux, cette longueur sera de 25 à 30 mm, une longueur souvent jugée trop courte par rapport aux attentes de la clientèle. Et si Variloc fonctionne bien en maïs, il n’est d’aucune utilité lors de l’ensilage de l’herbe à cause du taux de sucre plus élevé rendant l’herbe trop collante ».
La longueur de coupe oriente le choix de l’éclateur
Tout ceci est déterminant pour le choix suivant, celui de l’éclateur de grains. Il existe une relation étroite entre la longueur de coupe et le type d’éclateur ; plus la coupe est courte, plus il faut de dents sur l’éclateur. Toutes les marques proposent différentes solutions en matière de nombre de dents et de différentiel de vitesse de rotation entre les deux rouleaux.
« Aujourd’hui, la tendance est de pourvoir les deux rouleaux d’un nombre différent de dents ; les éclateurs avec 123 et 144 dents ou 105 et 123 dents ont la cote. Quant au différentiel de vitesse, il peut être modulé de 20 à 50 % », enchaîne Marc.
« Il est utile de rappeler que plus ce différentiel de vitesse est élevé, plus les grains sont éclatés. Cela satisfait l’éleveur dont les exigences sont de plus en plus pointues à ce niveau. Mais il y a un revers à cette médaille car cela use plus rapidement l’éclateur. Auparavant, il n’était pas rare de faire quatre saisons ou plus avec le même éclateur. Aujourd’hui, en conditions extrêmes, on peut n’en faire que deux… C’est une réalité que l’entrepreneur doit bien prendre en compte car ce sont des frais supplémentaires qui impactent la rentabilité de la machine ».
Les éclateurs à rouleaux équipent grosso modo 90 % des ensileuses belges ; d’autres sont pourvues d’un éclateur à disques, qui convient davantage aux coupes longues mais qui sont plus sensibles aux cailloux. Dans certaines situations, il est donc nécessaire de couper les tiges de maïs plus haut pour éviter de faire remonter des pierres dans la machine.
Deux outils additionnels : le pick-up à herbe…
Le premier outil est bien entendu le pick-up pour la récolte d’herbe. Comme le dit Marc : « Le pick-up est en soi un outil assez simple. D’ailleurs, lors d’un achat, autant on peut parler durant des heures avec le client du bec à maïs, autant on parle très pe
… et la table de coupe
De nombreuses options, à étudier au cas par cas
Il faut donc prendre le temps d’analyser toutes les possibilités car, en fonction des manufacturiers, il peut exister de petits écarts de taille qui font toute la différence en termes de gabarit routier. La plupart des constructeurs d’ensileuses proposent la possibilité d’une monte de chenilles mais cette solution n’est pas encore beaucoup ancrée dans les mentalités. Quant au télégonflage, il peut être très intéressant mais doit être réfléchi en fonction de la répartition des masses.
Si l’ensileuse évolue dans une région à forte densité de cailloux, il est opportun d’installer une protection du rotor adaptée lors de l’ensilage d’herbe. Des clients demandent par ailleurs l’incorporation d’additifs dans le produit ensilé. Il faut alors bien étudier les exigences de la clientèle pour opter pour le bon incorporateur.
Effectivement, selon que la demande porte sur des additifs à grand dosage ou des additifs en micro-doses, la régulation est la même mais les réservoirs sont différents et donc l’équipement également. « Il est aussi possible d’avoir un système d’injection d’eau pour la récolte d’herbe très collante. Cela peut se faire via le système d’injection d’additifs ou moyennant un autre dispositif », complète Marc.
Les options d’aide à la conduite, telles que le guidage automatique en maïs ou le pilotage automatique de la tuyère par caméra, ou les options de confort sont nombreuses chez les constructeurs. Ce sont des options qui méritent de faire partie de la réflexion car il ne faut pas oublier que le chauffeur passera de nombreuses et longues journées au volant de sa machine.
« Nous proposons depuis 2001 la suspension de l’essieu arrière. Cela apporte un véritable plus en matière de confort lorsque la vitesse d’avancement est relativement élevée comme lors des déplacements routiers ou de l’ensilage d’herbe. Je pense aussi à la cabine LiftCab qui permet d’élever la cabine de 70 cm. Si cela procure une meilleure visibilité en maïs, cela concourt aussi à réduire les nuisances sonores auxquelles est exposé le chauffeur car il s’éloigne des sources de bruit que sont le rotor, l’éclateur et le moteur. »
Pas à pas, organe après organe
Cet entretien avec Marc se termine sur une note de raison. « La réflexion au sujet de l’acquisition d’une nouvelle ensileuse se construit pas à pas, organe après organe, en fonction des réalités propres de l’entreprise, de sa clientèle, de sa région. Une fois les organes de travail choisis, le vendeur sera en mesure de remettre le prix de la machine de base ainsi constituée, que l’on pourra ensuite agrémenter de quelques options. »
« Au sujet de ces dernières, j’attire souvent l’attention de mes clients pour qu’ils optent pour des solutions qui leur seront réellement utiles. L’objectif est en effet de proposer la machine répondant au mieux aux besoins réels du client, et pas un engin bardé d’options dont on ne se sert jamais. C’est un point important, notamment en ce qui concerne la satisfaction du client mais aussi au niveau de son portefeuille. Pour en donner une idée, je me suis prêté au jeu : chez Krone, vous pouvez ajouter jusqu’à 175.000 € d’outils et d’options en tous genres sur une machine… »
« L’investissement doit toujours se faire en fonction de la clientèle, du potentiel et des moyens financiers à disposition de l’entreprise agricole. Bref, il doit être fait avec raison, même s’il n’est pas interdit de se faire plaisir de temps en temps ».
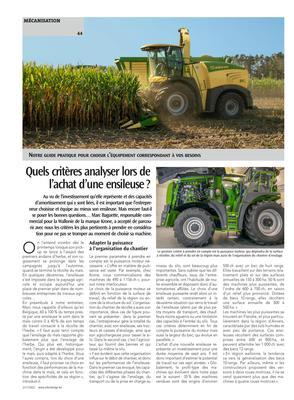